FAQ

Oplit
Advantages, exploitation, customization, measuring ROI...
See

Integration
Questions regarding the integration of Oplit with your already deployed solutions.
See

Data / Security
Questions related to the data necessary to operate Oplit, data flows, and their security.
See


Method / Glossary
Description of the CONWIP methodology, capacity loading plan...
See
Oplit
What is the difference between Oplit and an ERP?
A manufacturing ERP has features that allow for the management of a production site; however, its core business remains the management of resources, and the data it contains are statistical, often entered manually.
The core business of Oplit is the optimization of production flows and more specifically the optimization of the load-capacity balance, scheduling, and work-in-progress management. Oplit automatically collects data and consolidates it, making it an excellent communication tool, very collaborative.
A manufacturing ERP has features that allow for the management of a production site; however, its core business remains resource management, and the data it contains is statistical, often entered manually.
The core business of Oplit is the optimization of production flows and more particularly the optimization of load capacity balancing, scheduling, and work in progress management. Oplit automatically collects data and consolidates it, making it an excellent communication tool that is very collaborative.
What is the difference between Oplit and a MES?
Just like a MES, Oplit integrates with the ERP, however a MES will allow you to manage your resources and machines primarily (badge management, maintenance...), whereas Oplit will enhance the productivity of a site by optimizing its management of production flows, primarily acting on load-capacity balance, scheduling, and managing your work-in-progress.
Just like a MES, Oplit integrates with the ERP, however a MES will allow you to manage your resources and machines primarily (badge management, maintenance...), whereas Oplit will enhance the productivity of a site by optimizing its management of production flows, primarily acting on load-capacity balance, scheduling, and managing your work-in-progress.
What is the difference between Oplit and a ERP software?
If their core business is managing production flows, Oplit's expertise relies on its ability to optimize the balance between load and capacity, scheduling, and work-in-progress management. It also depends on its ability to provide flexibility and agility, as it is also an excellent communication tool for the entire production chain thanks to its capabilities in data management, consolidation, and sharing.
If their core business is managing production flows, Oplit's expertise relies on its ability to optimize the balance between load and capacity, scheduling, and work-in-progress management. It also depends on its ability to provide flexibility and agility, as it is also an excellent communication tool for the entire production chain thanks to its capabilities in data management, consolidation, and sharing.
Integration
How long does the implementation of Oplit take?
In general, the implementation of Oplit takes one to two months maximum. It will depend on the level of technical complexity as well as the resources available on the client side.
In general, the implementation of Oplit takes one to two months maximum. It will depend on the level of technical complexity as well as the resources available on the client side.
Does Oplit integrate with already deployed solutions?
Oplit is a SaaS (Software as a Service) solution, meaning it does not integrate tightly with its users' systems.
To operate, Oplit simply needs to communicate with the existing ERP via a CSV file or an API to receive basic data such as production inputs and outputs (item reference, production order reference, operation reference, load station, dates, etc.).
Implementations therefore happen fairly quickly over a duration of one to two months at most, including a testing phase managed by Oplit.
Finally, for security measures, Oplit never connects to the ERP. It is the ERP that sends data or makes requests to receive it.
Oplit is a SaaS (Software as a Service) solution, meaning it does not integrate tightly with its users' systems.
To operate, Oplit simply needs to communicate with the existing ERP via a CSV file or an API to receive basic data such as production inputs and outputs (item reference, production order reference, operation reference, load station, dates, etc.).
Implementations therefore happen fairly quickly over a duration of one to two months at most, including a testing phase managed by Oplit.
Finally, for security measures, Oplit never connects to the ERP. It is the ERP that sends data or makes requests to receive it.
Data / Security
Is Oplit coming to write in my ERP?
A bidirectional data flow of Oplit-ERP can be enabled. Oplit will then be able to retrieve any data, whether it is the capacity of the charging stations or the new end date of your work orders.
A bidirectional data flow of Oplit-ERP can be enabled. Oplit will then be able to retrieve any data, whether it is the capacity of the charging stations or the new end date of your work orders.
What data does Oplit need to function?
For Oplit to function, you will need to provide a file of charges, the production inputs and outputs made (article reference, OF reference, operation reference, cost center, dates, etc.) as well as your stock levels.
For Oplit to function, you will need to provide a file of charges, the production inputs and outputs made (article reference, OF reference, operation reference, cost center, dates, etc.) as well as your stock levels.
Method / Glossary
What is the CONWIP methodology?
The CONWIP (CONstant Work In Process) is a production management method in a pull flow system with constant work in progress.
CONWIP is used to reduce and control manufacturing lead times and to better meet customer deadlines.
The goal of the CONWIP method is to relay information that is available downstream, as quickly as possible, to the beginning of the production chain.
For example, once we receive information at station 3 that a product X needs to be produced, a ticket is sent to station 1 indicating that product E needs to be produced. This production will then be pushed up to station 3.
The CONWIP (CONstant Work In Process) is a production management method in a pull flow system with constant work in progress.
CONWIP is used to reduce and control manufacturing lead times and to better meet customer deadlines.
The goal of the CONWIP method is to relay information that is available downstream, as quickly as possible, to the beginning of the production chain.
For example, once we receive information at station 3 that a product X needs to be produced, a ticket is sent to station 1 indicating that product E needs to be produced. This production will then be pushed up to station 3.
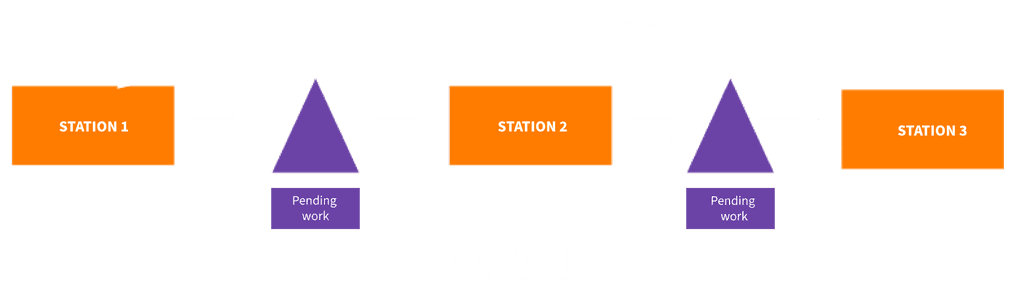
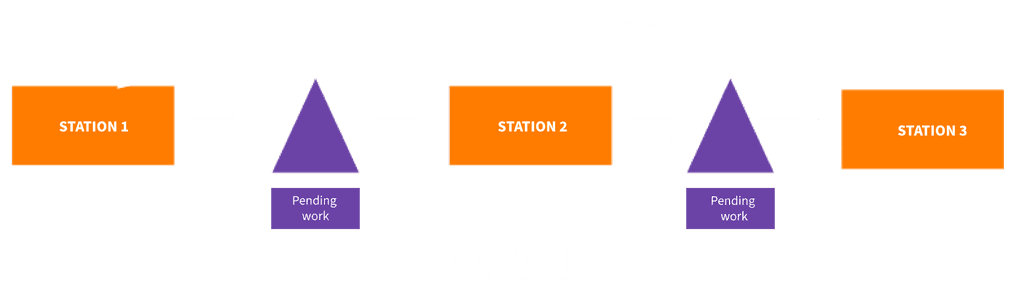
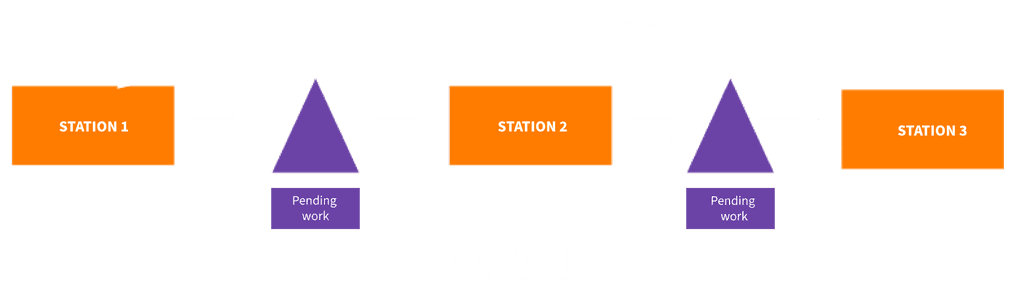
Each ticket is generic, meaning they are assigned to a specific OF.
Once this OF is completed, the ticket becomes blank again.
If we take our example, once product X is completed at station 3, the CONWIP ticket becomes blank and is ready to accept a new type of product to be produced (in our case, product E). The ticket is then returned to the beginning of the line or to the previous buffer. This ticket then constitutes an OF.
As long as there is no blank ticket on the CONWIP board, the entry of new OFs on the line is not allowed. And we can segment the production line based on the identified buffers. This allows for multiple CONWIP flows on the chain.
Each ticket is generic, meaning they are assigned to a specific OF.
Once this OF is completed, the ticket becomes blank again.
If we take our example, once product X is completed at station 3, the CONWIP ticket becomes blank and is ready to accept a new type of product to be produced (in our case, product E). The ticket is then returned to the beginning of the line or to the previous buffer. This ticket then constitutes an OF.
As long as there is no blank ticket on the CONWIP board, the entry of new OFs on the line is not allowed. And we can segment the production line based on the identified buffers. This allows for multiple CONWIP flows on the chain.
What is a capacity load plan or PDP?
The PDP is a medium-term program lasting from 1 to 6 months (2 to 3 production cycles).
It allows defining the production needs for each individual and finished product (taking into account management rules and the schedule of various needs) to meet demand and anticipate balancing decisions based on available resources and load.
It must be updated daily to consider stock levels and new logistical constraints such as supplier lead times.
The master production plan is based on the Industrial and Commercial Plan (PIC). The PIC is a long-term vision of 1 to 3 years depending on the line of business and is updated monthly or quarterly. It sets broader objectives for product families.
Once the PIC is established, the PDP allows for detailing the needs for finished products item by item, consistent with past production.
Such production planning brings together production teams and the supply chain around a common goal for the weeks and months to come.
This production or load objective being known thanks to the PDP, one can verify that it balances with production capacity.
Thus, a good master production plan will prevent not only significant costs such as machine rentals or last-minute labor shifts if the load is too high, but also a substantial loss of revenue if capacity is too high and units are not utilized.
The PDP is a medium-term program lasting from 1 to 6 months (2 to 3 production cycles).
It allows defining the production needs for each individual and finished product (taking into account management rules and the schedule of various needs) to meet demand and anticipate balancing decisions based on available resources and load.
It must be updated daily to consider stock levels and new logistical constraints such as supplier lead times.
The master production plan is based on the Industrial and Commercial Plan (PIC). The PIC is a long-term vision of 1 to 3 years depending on the line of business and is updated monthly or quarterly. It sets broader objectives for product families.
Once the PIC is established, the PDP allows for detailing the needs for finished products item by item, consistent with past production.
Such production planning brings together production teams and the supply chain around a common goal for the weeks and months to come.
This production or load objective being known thanks to the PDP, one can verify that it balances with production capacity.
Thus, a good master production plan will prevent not only significant costs such as machine rentals or last-minute labor shifts if the load is too high, but also a substantial loss of revenue if capacity is too high and units are not utilized.
Book your personalized demo
You are launching a digitalization project for your production planning, so schedule some time to discuss with us. We will show you how Oplit can help you,
you and your entire production chain.
Schedule a demo